步是钢格板焊接,将开裂、损坏的当地进行钢格板焊接,第二步是将焊接点进行打磨,要求是焊接点与附近当地平坦,第三步是酸洗,这一点要严厉操作, 要是剂量过大就会产品。
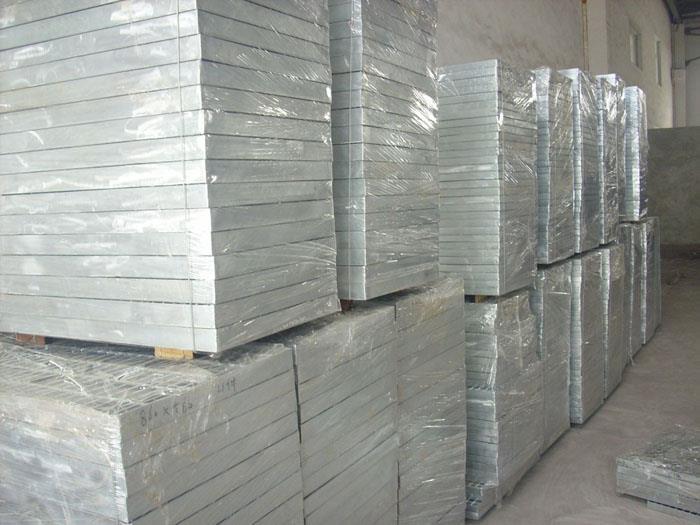
我公司在实际生产过程中根据多个项目总结,通过CFD模拟实验,整理了一套关于整流格栅对锅炉脱销效果的具经验:
1、整理格栅的间距越大,其下游烟流入射角度越大,烟分布均匀性越差,能满足指标要求的反应器内截面积高度越低,可接受的首层催化剂的安装位置越靠下,整流格栅间距小于120㎜为可接受的设计参数设计。
2、将靠近烟气侧的整流格栅设计为倾斜结构可缓解反应器中靠近气侧的流速偏低现象。提高烟气流速均匀性。并且整流格栅间距越小,次改进方式的效果越明显。一、承载以及使用范围。
首先我们对烟气脱硝进行一个简单了解。
烟气脱硫: 根据吸收剂及脱硫产物在脱硫过程中的干湿状态,火力发电行业一般将脱硫技术分为湿法、干法和半干(半湿)法。
(1)湿法烟气脱硫技术是用含有吸收剂的浆液在湿态下脱硫和处理脱硫产物,该方法具有脱硫反应速度快、脱硫效率高、吸收剂利用率高、技术成熟可靠等优点,但也存在初投资大、运行维护费用高、需要处理二次污染等问题。应用多的湿法烟气脱硫技术为石灰石湿法,如果将脱硫产物处理为石膏并加以回收利用,则为石灰石-石膏湿法,否则为抛弃法。 其他湿法烟气脱硫技术还有氨洗涤脱硫和海水脱硫等。
(2)干法烟气脱硫工艺均在干态下完成,无污水排放,烟气无明显温降,设备腐蚀较轻,但存在脱硫效率低、反应速度慢、石灰石利用率较低等问题,有些方法在设备大型化的进程中困难很大,技术尚不成熟(主要有炉内喷钙等技术)。
半干法通常具有在湿态下进行脱硫反应,在干态下处理脱硫产物的特点,可以兼备干法和湿法的优点。主要包括喷雾干燥法、炉内喷钙尾部增湿活化法、烟气循环流化床脱硫法、电子束辐照烟气脱硫脱氮法等。 迄今为止,世界各国已开发出多种治理烟气中氮氧化物的方法,其中以选择性催化还原法(SCR)技术为成熟,脱硝效率,并已在大型燃煤电厂获得广泛应用。
整流格栅平台要求具备通风透气,承载性高的要求。热镀锌钢格栅板恰恰是蒸馏脱硝平台不可缺少的建材产品。在各大电厂采购的格栅板当中G325/30/100w这种格栅是需求量的。G325/30/100W这种格栅表面热镀锌,能够程度的耐腐蚀。同时还能单位平米内承载400KN的能力。
上面说到了整流格栅平台上次经常采用的格栅板,那整流格栅通常用的是什么规格的? 整流格栅材质一般为Q345材质,具备的耐磨性和承载能力,在我国国内采用的整流格栅一般高度为300mm。网孔110mm/321mm之间,板板之间采用开孔插接满焊的方式生产。脱销整流格栅的生产过程要求生产企业具备大型的冲床、大型吊装设备和技术娴熟的焊接工人,只有这样才能生产出合格的整流格栅产品。
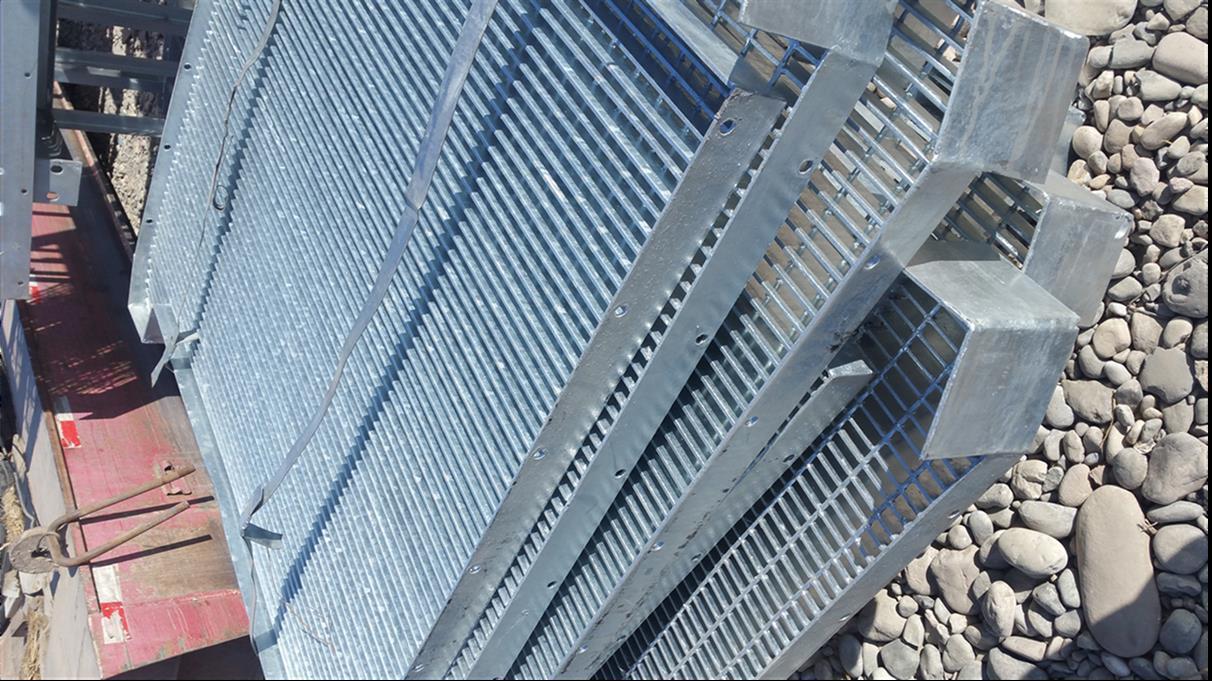
平台整流格栅在长期的使用过程中难免会出现损坏,如何修复损坏的平台钢格板?今天就和大家一起简单分析一下平台钢格板是如何修补的呢?在没有防护情况下的平台整流钢格板,很简略生锈、易变旧,使其钢格板使用寿命缩短,就算是养护好的钢格板商品,使用一段时间后也会损坏的,所以我们要定时对平台钢格板做一下修补。
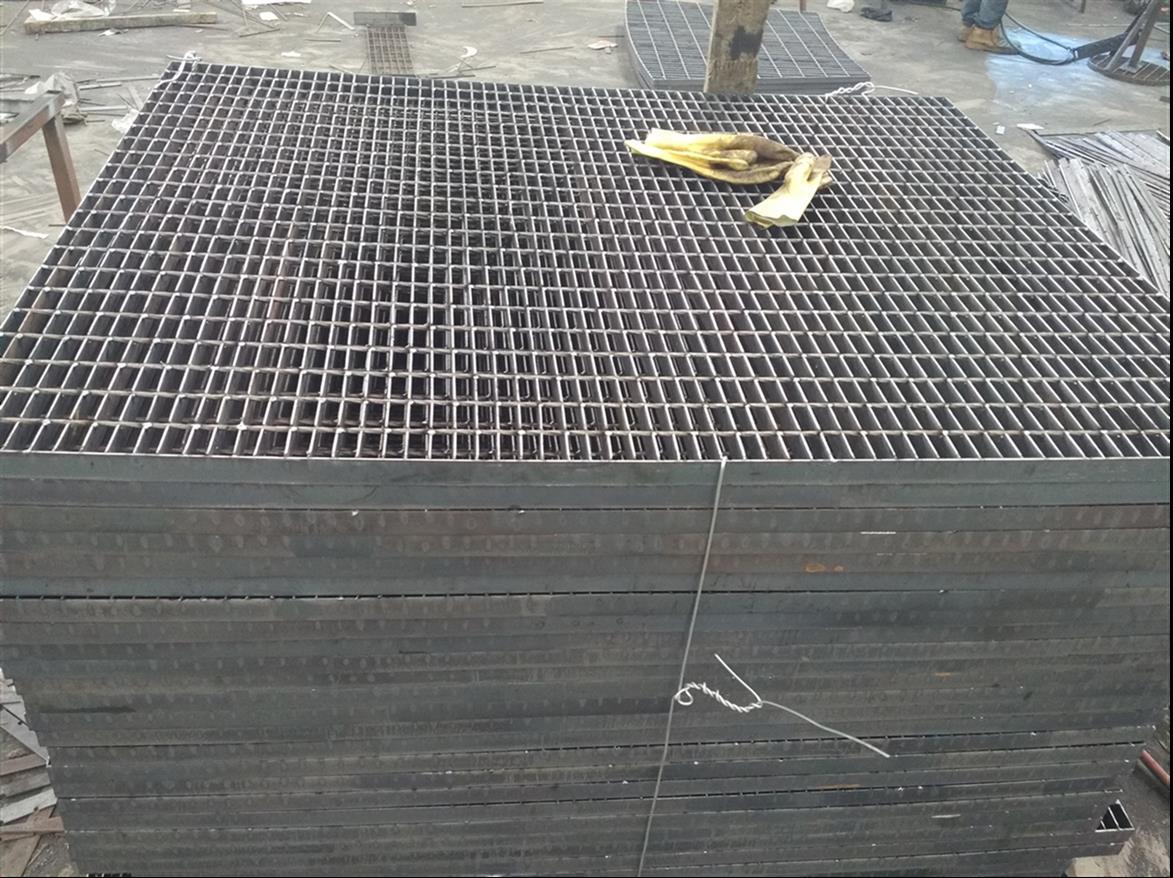
无锡整流格栅工业发达,发展迅速,国家近几年大力开展环境保护,控制大气污染,要求各石油化工、电厂、矿场对燃煤脱硫脱硝防止空气污染提出了新的要求。那么这个过程中就少不了整流格栅的使用。
脱硝反应器内流场均匀与否关系到脱硝系统的实现,而决定反应器内流场均匀性的关键在于催化剂床层上部导流装置的性能。应用计算流体力学软件CFD,通过改变导流板间距、导流板长度、与Z轴的夹角(垂直轴)以及第1块导流板距反应器边壁的距离,对烟气整流格栅进行模拟,从而分析烟气整流格栅结构参数对反应器流场分布的影响。结果表明,第1块导流板距反应器边壁距离的改变对流场性能影响很弱,可以忽略;各结构参数取值存在一个使反应器流场的范围;原始方案在均匀性、烟气速度矢量指标、压降中均优,可作为设计基准。
整流格栅主要用用在电厂烟道脱硫脱硝中,承载力强,过滤好,通风透气,现已逐步应用于电厂中。一般采用 300*3mm扁钢,选用100*100mm的方格,扁钢与扁钢互插而成,尺寸各异,一般长度较长,达到10米左右。由于其长度较长,加工制作周期较长,建议客户采购时能提前订货。
基于CFD模拟软件对某SCR脱硝装置进行了数值模拟,分析了不同整流格栅间距、形式对反应器上部流场的影响。以不同高度截面的烟气速度变异系数CV和气入射角为定量评价指标,给出了满足性能要求的整流格栅设计参数范围以及优设计方案。
整流格栅是SCR脱硝系统中重要的功能部件,其作用一是通过烟气在格栅内的碰撞、整合作用,将进入格栅前水平方向流动的烟气调整为竖直向下流动,其二是将进入格栅前较差的烟气速度分布整合的相对均匀。这两个作用对于SCR脱硝系统而言具有重要的意义,烟气在催化剂前控制在一定范围内的入射角能够避免催化剂表面被过渡冲刷,使催化剂寿命得到**,而速度分布的均匀性则是催化剂能被充分利用,达到理想脱硝效率的关键。因此,对SCR脱硝系统中整流格栅的结构进行优化设计十分必要。
本文对某300MW机组的SCR装置进行了数值模拟,通过改变整流格栅的间距及其形式,分析了不同整流格栅结构对其下游烟气分布和烟气入射角的影响,给出了可以满足性能需求的设计范围及优方案,对于整流格栅的优化设计有一定参考价值。
1数值模拟
采用三维建模软件建立与实际装置等比例的几何模型,建模范围为SCR进口至反应器出口,如图1所示。由于导流板及整流格栅的厚度远小于反应器及烟道尺度,故建模时将其厚度忽略。网格划分时,Z向平面网格采用结构化与非结构化结合的方式划分,然后由Cooper方式生成体网格,终网格总数约为250万。
数值计算采用Fluent软件,湍流模型选用标准k-ε双方程模型,氨气与烟气的混合过程采用SpeciesTransport模型,边界条件设置为速度进口与压力出口。根据烟气参数和装置尺寸,设置进口速度为12m/s,进口温度为660K,水力直径为4.5m;AIG喷口速度为8.4m/s,水力直径为3.2m;反应器出口水力直径为4m。本文计算不考虑催化剂层阻力。
图1SCR脱硝装置几何模型
2定量分析
首层催化剂上游的速度入射角度、烟气及氨气浓度分布均匀性是保证脱硝性能的关键因素。采用变异系数CV对速度及浓度的均匀性作定量分析,其定义是标准偏差与算术平均值之比,可反映出一组测量数据的离散程度。就本文而言,CV越明截面上速度或浓度的分布越均匀,偏离平均值的数据点越少。烟气入射角即烟气偏离垂直向下方向的角度,将该角大值α作为速度矢量的定量分析指标。对于速度CV、浓度CV以及α的优化目标如表1所示。
表1 CFD流场模拟定量分析指标
需要说明的是,由于氨气浓度CV的大小主要取决于AIG上游的烟气速度分布,控制其大小的措施是通过合理布置导流板优化AIG上游流场,与整流格栅的形式变化关系不大,因此下文对整流格栅结构的优化将以速度CV和大入射角α作为指标,在终确定的优方案中将给出完整的定量指标结果。
http://www.cn-y.cn